【製作事例も紹介】板金筐体の製作工程
板金筐体とは
板金筐体は、金属板を加工して作られる筐体で、電子機器や機械装置の外装や内部構造に広く使用されています。
筐体は「ボックス」、「ケース」、「ラック」、「ハウジング」、など様々な呼び方があります。
軽量でありながら強度が高く、加工の自由度が高いため、さまざまな形状やサイズに対応できます。
特に、カスタマイズが容易であるため、特定の用途に合わせた設計が可能です。
また、耐久性や耐食性に優れているため、長期間にわたって使用することができます。
板金筐体製作の加工工程とは
板金筐体の製作は複数の加工工程があります。
以下に、その主要な工程を詳細にご紹介します。
⓵設計
板金筐体の製作は、まず設計から始まります。
設計者は、使用目的や要求仕様に基づいて、CADソフトウェアを使用して詳細な図面を作成します。
この段階では、材料の選定や寸法の決定、組み立て方法の検討が行われます。
設計の精度が製品の品質に直結するため、非常に重要な工程です。
また、3Dモデリングを活用することで、製品の完成形を視覚的に確認し、設計ミスを未然に防ぐことができます。
②ブランク加工
設計が完了したら、次にブランク加工が行われます。
ブランク加工とは、金属板を所定の形状に切り出す工程です。
当社では、主にレーザー切断と金型によるパンチ加工で切り出しを行います。
これらの切断方法は、材料や形状に応じて使い分けます。
例えば、レーザー切断は高精度で複雑な形状の切断に適しており、パンチ加工は加工スピードが早く安定した加工ができるため量産向けの製品などに適しています。
レーザー切断や金属板を切り出した後、金属板に穴を開けたり、特定の形状に切り抜いたりする工程があります。
この工程は、タレパン複合機(全自動タレットパンチ&レーザー複合機)、プレス機やパンチングマシンを使用します。
ブランク加工は、製品の機能性を確保するために重要な工程であり、精度が求められます。
③曲げ加工
抜き加工が完了した金属板は、曲げ加工に進みます。
曲げ加工では、金属板を所定の角度に曲げて、立体的な形状を作り出します。
曲げ加工は、ベンディングマシンやプレスブレーキを使用しますが、曲げ加工は製品の強度や形状を決定する重要な工程であり、曲げ角度や曲げ半径の精度が求められます。
また、曲げ加工の際には、金属の特性を考慮して適切な加工条件を設定することが重要です。
④溶接加工
曲げ加工が終わった部品は、溶接加工によって組み立てられます。
溶接はTIG溶接、スポット溶接、ファイバーレーザー溶接などの方法があります。
溶接加工は、製品の強度や耐久性を確保するために重要な工程であり、溶接の品質が製品の寿命に大きく影響します。
例えばアルミのような熱伝導率の高い金属の溶接では、ファイバーレーザー溶接を行うことでひずみにくい高精度な加工ができます。
当社では、全自動のファイバーレーザー溶接機に加えて、ハンディファイバーレーザー溶接機を2台保有しておりますので、様々な形状でも対応できます。
また、溶接後には、溶接部の検査や仕上げ加工が行われ、品質、美麗外観を確保します。
⑤組み立て
溶接加工が完了したら、次に組み立て工程に進みます。
組み立て工程では、必要な部品やコンポーネントを取り付けて、最終的な形状に仕上げます。
ネジやボルト、リベットなどを用いて組み立てを行います。
組み立て工程では、各部品の位置や取り付け方法が正確であることが求められ、製品の機能性や信頼性に直結します。
また、組み立ての際には、製品の動作確認や調整が行われ、最終的な品質が確保されます。
⑥配線
組み立て工程と同時進行で配線作業も行います。配線工程では、配線を安全に動作するように、電源ケーブル、信号ケーブル、接地ケーブルなどの配線設計を行います。また、用途に応じて適切な材質のケーブルを選定する必要があります。
最適な配線設計をしていないと、無駄な配線が必要になることや、熱をもってしまったり、破損してしまったりという不具合に繋がります。
また医療機器用の筐体などでは、精密な検査データを扱うため、電磁干渉(EMI)などを最小限に抑えた配線設計をする必要があります。
⑦塗装・表面処理
組み立てが完了した板金筐体は、塗装やメッキ、シルク印刷等の表面処理が施されます。
塗装では、筐体の外観を美しく仕上げるとともに、耐久性を向上させます。
粉体塗装や溶剤塗装、電着塗装などの方法が使用されます。
表面処理では、錆や腐食を防ぐための処理が行われ、製品の寿命を延ばします。
また、塗装や表面処理の工程では、環境に配慮した材料や方法が選ばれることが多く、持続可能な製造が求められます。
⑧検査・出荷
完成した板金筐体は、寸法検査や外観検査、機能検査などを行い、不良品がないことを確認します。
当社では、各加工工程ごとに検査を行っているため、組み立て後では見えないような箇所も検査を行っております。
検査工程では、製品の品質を確保するために厳密な基準が設けられており、製品の信頼性を高めるために重要です。
また、出荷前には、キズや変形に配慮した製品の梱包や輸送方法が検討され、安全に皆様のもとへ届けられるように配慮されます。
このように板金筐体の製作過程は、多くの工程で形成されていますが、それぞれの工程が緻密に連携した高品質な製品に仕上げるために重要です。
当社の板金筐体 設計・製作サービスの3つの特長
当社の板金筐体の設計・製作サービスの3つの特徴をご紹介します。
⓵試作・量産に合わせた、設計段階からのコストダウンご提案
精密筐体フレーム・ファクトリーを運営する佐藤電機製作所では、お客様に対して、材質や加工方法の変更提案、図面を頂いた段階での最適な設計変更提案などの品質向上・加工コスト削減、納期短縮につながるような改善提案を積極的に行っています。細かい改善提案を含めると、年間100件以上の提案実績があり、試作・量産等の様々なタイミングに合わせた、ご提案をさせていただきます。
②最新設備の使用による安定した加工品質
精密筐体フレーム・ファクトリーを運営する佐藤電機製作所では、板金加工における曲げ・レーザー・プレス、溶接加工から、メッキや塗装、印刷、部材調達、組立、出荷まで一貫して生産できる体制を構築しております。
さらに、図面を頂いたら、図面のデータ化を行い、各工程ごとにそのデータを用いて生産管理を行っています。それにより、蓄積したデータを活用し、最適な加工を実施できるため、安定した品質かつ、コストを抑えた加工を行うことが可能です。
③安定した生産体制を構築による多品種少量生産
精密筐体フレーム・ファクトリーを運営する佐藤電機製作所では、西関東随一の最新鋭の設備を保有しており、さらに、図面の電子化により全社員がデータをタブレットで見える化もしています。
また、生産管理システムにより工程の進捗管理もしているため、回答納期遵守率97%を実現しております。 それにより、常に安定した生産体制を構築することができ、超多品種少量生産を実現しています。
10~100個の製作の場合は、最適コスト・短納期で対応することが可能です。
>>当社の当社の板金筐体 設計・製作サービスについて詳しく知りたい方はこちら
当社の板金筐体事例をご紹介!
事例1 医療機器用シャーシ製作事例
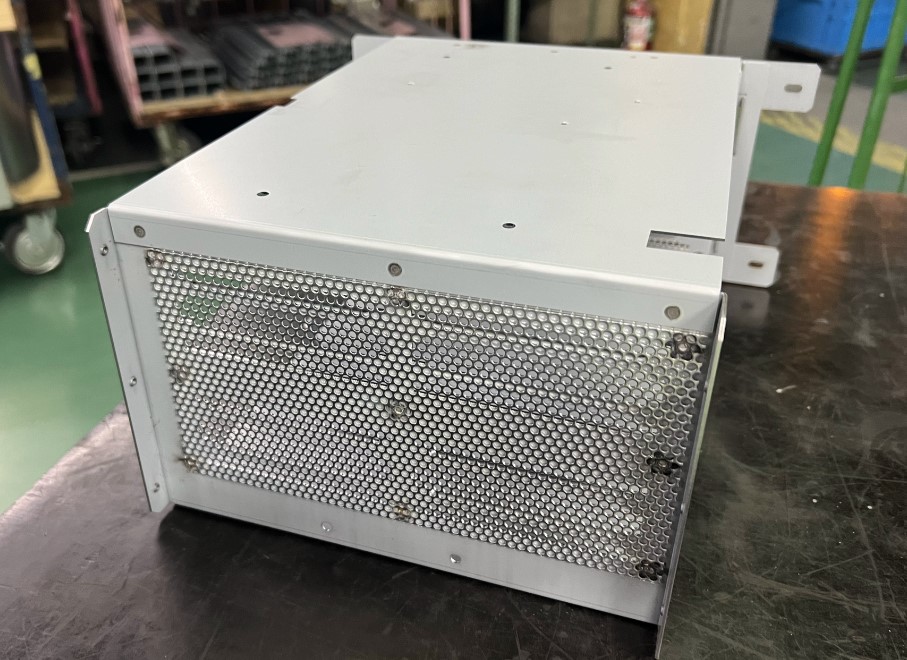
こちらは、シャーシの製作事例です。
こちらは、パンチングメタルを抜く作業から曲げ加工、スポット溶接まで、一貫して製作しております。
材質やパンチングメタルによっては、スポット溶接しづらい場合がありますが、当社ではスポット溶接の実績が豊富にあるため、対応可能です。
事例2 検体前処理装置 SECC筐体
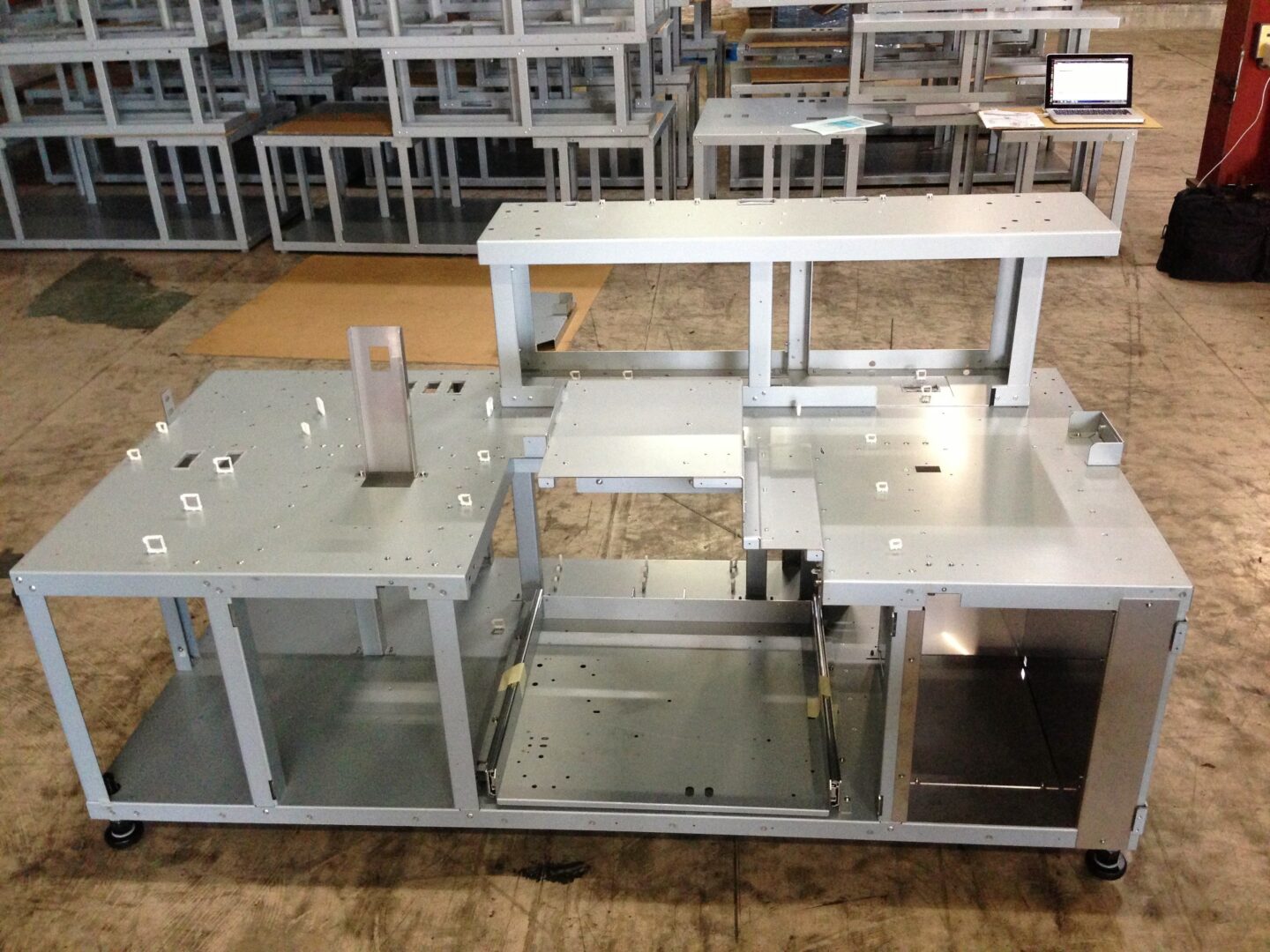
こちらは、検体前処理装置の筐体です。
検体前処理装置筐体は、内部の電子機器を保護し、操作や診断の効率、強度を高めるため慎重に設計をしました。
筐体の接合部は主にリベットを使用しており、強度が必要な箇所は溶接構造を採用しています。
ただし、全体を溶接構造にすると、歪みや作業時間増加により、コストアップに繋がるなどのデメリットが発生するため、基本的にはリベット構造を選択しております。
また、製品の組立作業においては、データや写真を用いたIT管理が活用されており、複雑な製品の組立が迅速かつ安定して行われることが可能です。
事例3 超音波診断装置 SECC筐体
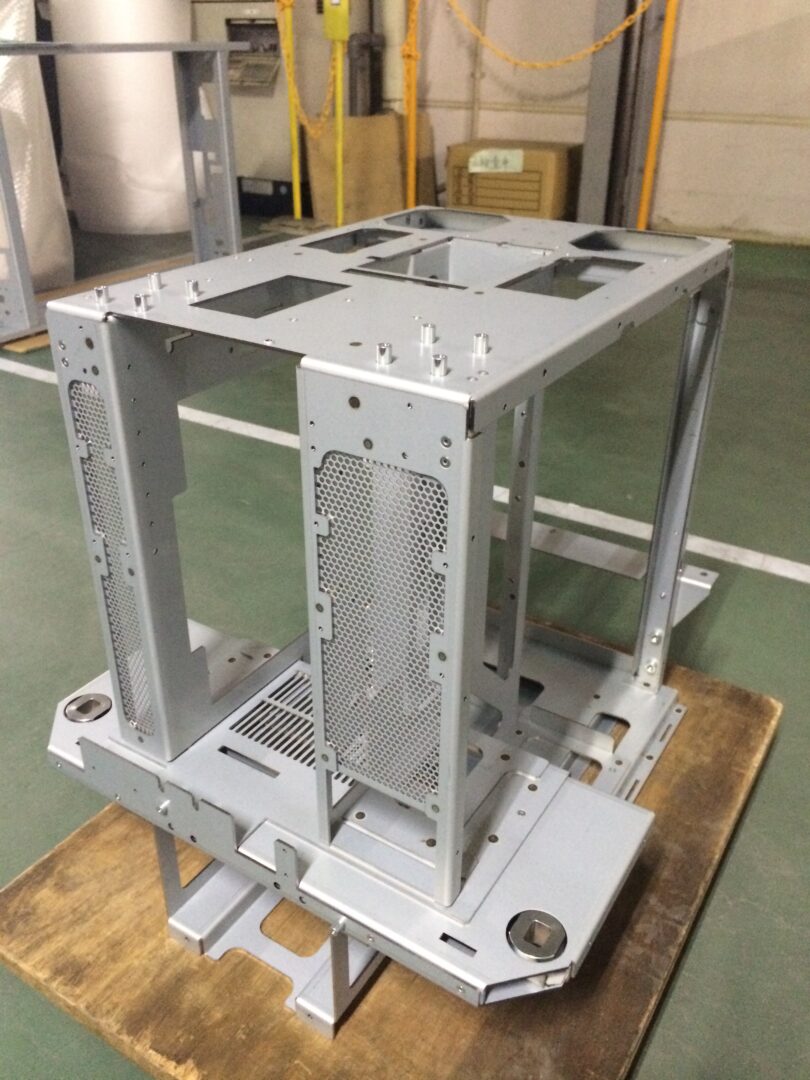
こちらは、超音波診断装置筐体です。
超音波診断装置の筐体は、医療機器として使用され、装置の内部を保護し、検査の正確性と信頼性を確保するために重要な役割を果たします。
また、使いやすさだけではなく、機能性も求められるため、清潔さと衛生面に考慮した設計をしております。
最後に
いかがでしたでしょうか。本記事では、筐体向けの精密板金加工の設計・製作における重要なポイントと、当社の板金筐体の製作事例を、ご紹介しました。
精密板金筐体・フレームファクトリーを運営する佐藤電機製作所では、板金筐体をはじめとした精密板金加工を得意としております。
当社が行ったVA/VE事例を掲載しておりますので、是非一度ご覧ください。
板金筐体・フレーム等の板金加工品のお悩み・ご相談があれば、一度お問い合わせください。