図面に起因して起こる筐体製作のトラブルと解決策
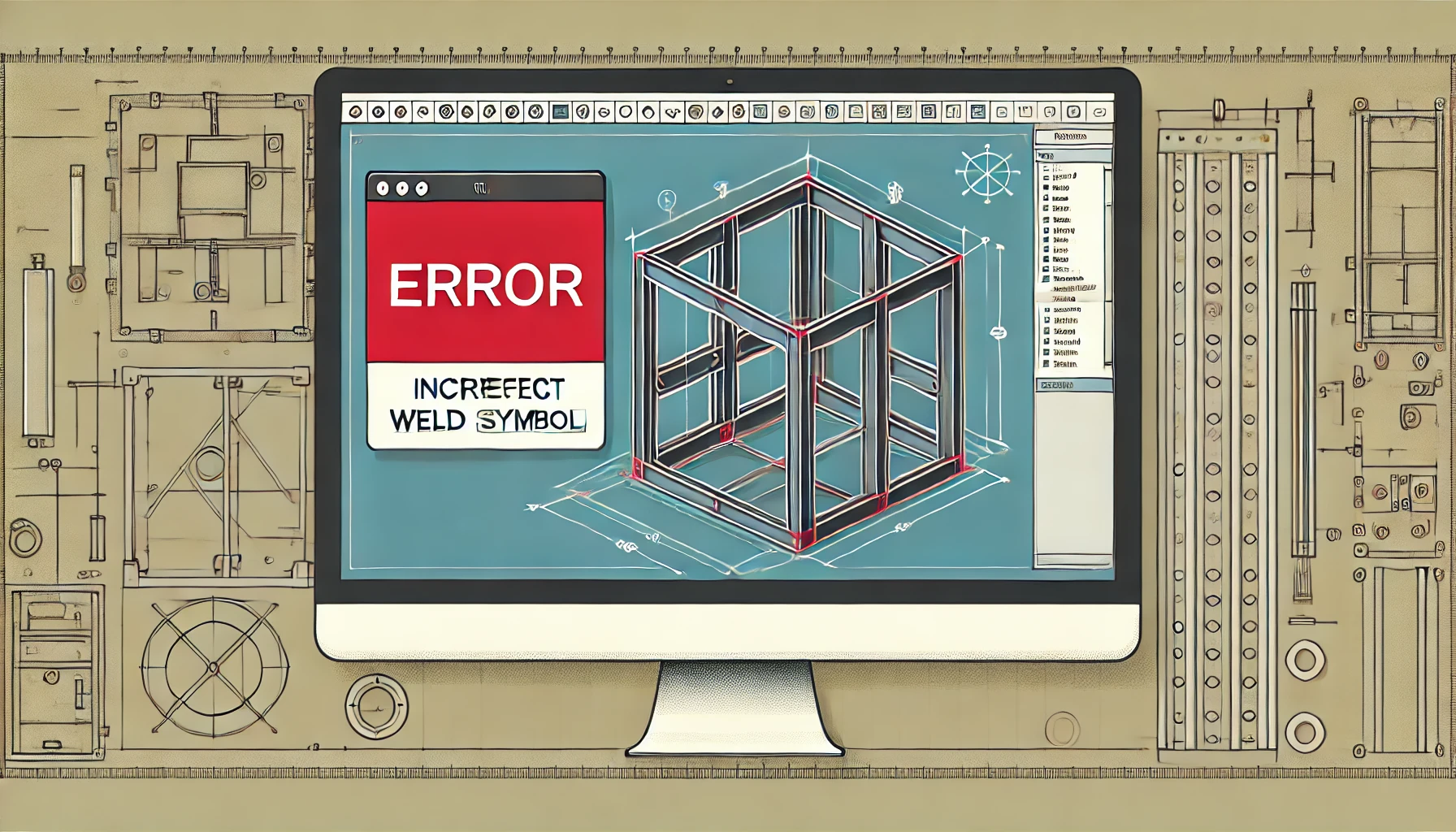
筐体製作において、図面は設計者の意図を製造現場に伝えるための重要なコミュニケーションツールです。しかし図面が、製作側に誤った解釈を与え得るものになっていると、製作する筐体が設計者の意図と異なるものとなり、様々なトラブルを引き起こす可能性があります。ここでは、図面の書き方等によって発生するトラブルと、その解決策について詳しく解説します。
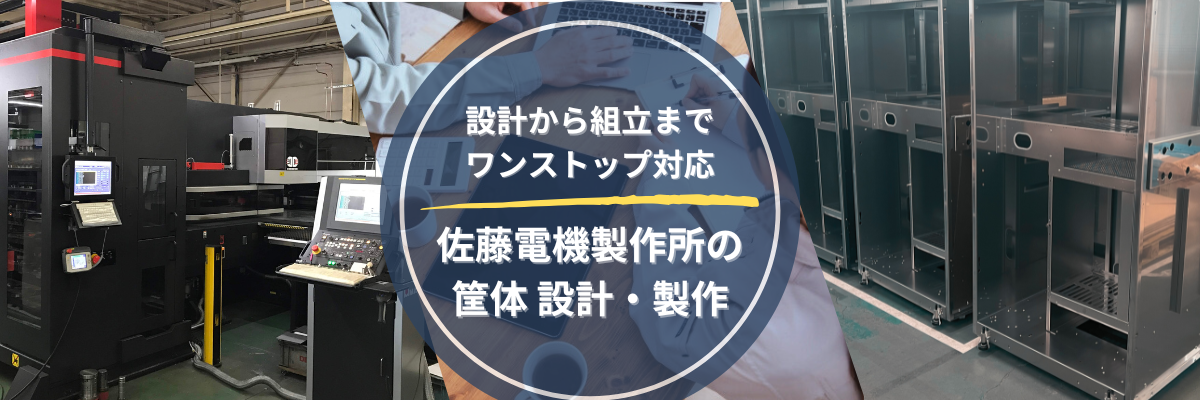
図面解釈の誤りによる問題点
図面解釈の誤りは、筐体製作の様々な段階で問題を引き起こす可能性があります。主な問題点としては、以下のようなものが挙げられます。
寸法誤差
図面に記載された寸法を設計側のイメージ、意図とは異なる解釈を行い、実際の製作寸法が設計意図と異なる場合、内部装置や配線組立時に部品同士の隙間や干渉が発生する可能性があります。これは、筐体の組み立て不良や機能不良、さらには安全性に関わる重大な問題に発展する可能性もあります。
形状誤差
図面に示された形状を誤って解釈し、実際の製作形状が図面と異なる場合、筐体の外観不良や機能不良、他の部品との干渉などが発生する可能性があります。
材質誤差
図面に指定された材質を誤って解釈し、異なる材質で筐体を製作した場合、筐体の強度不足や耐食性不足、重量変化などが発生する可能性があります。
表面処理誤差
図面に指定された表面処理を誤って解釈し、異なる表面処理を施した場合、筐体の外観不良や耐食性不足、機能不良などが発生する可能性があります。
加工方法誤差
図面に指示された加工方法を誤って解釈し、異なる加工方法で製作した場合、筐体の精度不良や強度不足、外観不良などが発生する可能性があります。
これらの図面解釈の伴う誤りは、筐体の品質や機能、さらには納期やコストにも悪影響を及ぼす可能性があります。最悪の場合、製品のリコールや事故に繋がることもあり、設計者と製作側は図面解釈の重要性を十分に認識しておく必要があります。
図面解釈の誤りが発生する原因
図面解釈の誤りは、様々な要因が複雑に絡み合って発生します。主な原因としては、以下のようなものが考えられます。
1. 図面自体の問題点
図面の記載不備: 寸法や形状、材質、表面処理などの情報が図面に十分に記載されていない場合、あるいは一般的な表記と異なる表記等の場合、製作側の解釈の誤りが発生しやすくなります。
図面の表現方法: 図面の表現方法が分かりにくく、誤解を招きやすい場合、解釈の誤りが発生する可能性があります。
図面記号の理解不足: 図面に使われている記号の意味を設計者が正しく理解していない場合、解釈の誤りが発生しやすくなります。例えば幾何公差の記号、定義等において起こることも多く、円筒度と真円度を混同している等が実際の例としてあります。
2. 図面解釈者の問題点
経験不足: 製作側が、慣れている既存取引先以外の図面解釈の経験が少ない場合、図面の情報を正しく読み取る能力が不足し、誤った解釈をしてしまう可能性があります。
注意力不足: 図面を注意深く確認せず、見落としや思い込みによって誤った解釈をしてしまう場合があります。
3. コミュニケーション不足
設計者と製作現場との意思疎通不足: 設計者と製作現場の間で、図面に関する十分なコミュニケーションが行われていない場合、あるいはコミュニケーションを行うことが困難な場合(間に別の会社が入っている場合等)、解釈の誤りが発生しやすくなります。
情報共有の不足: 図面に関する情報や変更履歴などが関係者間で共有されていない場合、誤った情報に基づいて製作が行われる可能性があります。
図面解釈の誤りを防ぐための解決策
図面解釈の誤りを防ぎ、設計者の意図通りの筐体を製作するためには、以下の対策を総合的に実施することが重要です。
1. 図面作成段階における対策
図面情報の明確化: 寸法、形状、材質、表面処理、加工方法など、必要な情報を図面に漏れなく、明確に記載することが重要です。製品の設計開発には、デザイン、人間工学、コスト面などを考慮する必要があります。
分かりやすい図面表現: 図面の表現方法を工夫し、誰が見ても誤解なく理解できるようにすることが重要です。図面には内寸と外寸があるので、注意が必要です。内寸で表記されている図面は外寸に書き換えることで、寸法間違いを防ぐことができます。
図面記号の統一: 図面記号は、JISなどの規格に準拠したものを使い、社内でも統一することで、誤解を防ぐことができます。
3Dデータの活用: 2D図面だけでなく、3Dデータも併用することで、形状や構造をより正確に伝えることができます。
チェック体制の強化: 図面作成後には、複数人でチェックを行い、記載ミスや表現の分かりにくさなどを修正することが重要です。
2. 図面解釈者に対する教育
図面解釈研修: 図面解釈の基礎知識や、図面記号の意味、図面の見方などを学ぶ研修を実施することで、図面解釈能力の向上を図ります。
経験豊富な担当者による指導: 経験豊富な担当者から、図面解釈のポイントや注意点などを指導してもらうことで、実践的な知識を習得することができます。
最新情報の共有: 図面に関する規格や標準、新しい技術など、最新の情報 を共有することで、常に正しい知識に基づいて図面解釈を行うことができます。
3. コミュニケーションの促進
設計者と製作現場の連携強化: 設計者と製作現場が密接に連携し、図面に関する疑問点や不明点を解消することで、解釈の誤りを防ぐことができます。外注委託の場合、融通がきかない、レスポンスが遅いなど、連携力が問題になることも多々あります。
ミーティングの実施: 図面に関するミーティングを実施し、設計意図や製作上の注意点などを共有することで、双方の理解を深めることができます。技術資料を送付してもらい、技術内容に関する問い合わせにも回答してもらうことができます。
情報共有システムの導入: 図面データや変更履歴などを一元管理できるシステムを導入することで、情報共有の遅れや不足を防ぐことができます。
4. 図面解釈支援ツールの活用
CAD/CAMシステム: CAD/CAMシステムの中には、図面解釈を支援する機能が搭載されているものがあります。これらの機能を活用することで、寸法や形状などを正確に把握することができます。
シミュレーションソフトウェア: シミュレーションソフトウェアを使用することで、組立工程などを事前に確認し、図面解釈の誤りによる問題を未然に防ぐことができます。
図面解釈の誤りが発生した場合の対応
図面解釈の誤りが発生した場合、迅速かつ適切な対応が必要です。
問題の深刻度や影響範囲に応じて、以下の対応策を検討します。
1.修正・再製作: 誤りが軽微な場合は、修正や再製作で対応できる場合があります。
2.設計変更: 誤りが設計に起因する場合は、設計変更が必要となる場合があります。
3.工程見直し: 誤りが製作工程に起因する場合は、工程の見直しや作業者の再教育などが必要となる場合があります。
誤りが発生した場合、以下の手順で対応することが重要です。
1.問題点の正確な把握: 発生した問題点の内容、影響範囲、発生原因などを正確に把握します。
2.関係者への報告: 発生した問題点と対応方針を、関係者(設計者、製作担当者、顧客など)に報告します。
3.対策の実施: 状況に応じて、修正、再製作、設計変更、工程見直しなどの対策を実施します。
4.再発防止策の検討: 同じ誤りが再発しないよう、図面作成方法、解釈方法、コミュニケーション方法などを見直し、再発防止策を検討します。
まとめ
図面解釈の誤りは、筐体製作において重大な問題を引き起こす可能性があります。図面作成者、解釈者双方からの対策、そして円滑なコミュニケーションによって、誤りを防ぎ、高品質な筐体製作を実現することが重要です。