溶接不良が引き起こす問題と対策
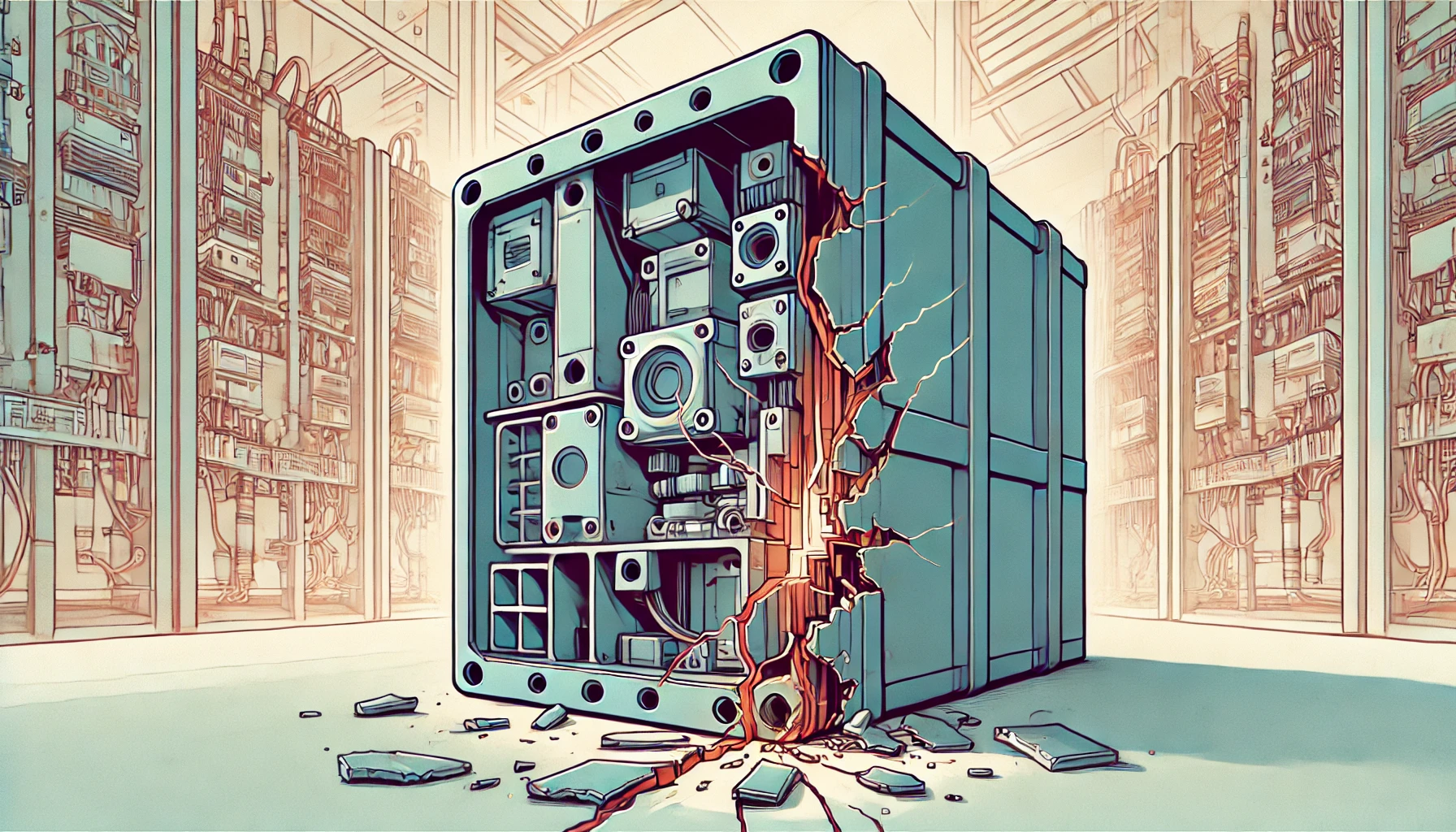
溶接は、金属部品を接合する重要な加工技術であり、筐体製作においても広く用いられています。しかし、溶接は適切な条件で行わないと、溶接不良が発生し、筐体の強度や耐久性、外観を損なうだけでなく、重大な事故につながる可能性も孕んでいます。本稿では、溶接不良によって発生する問題点とその対策について、詳細に解説します。
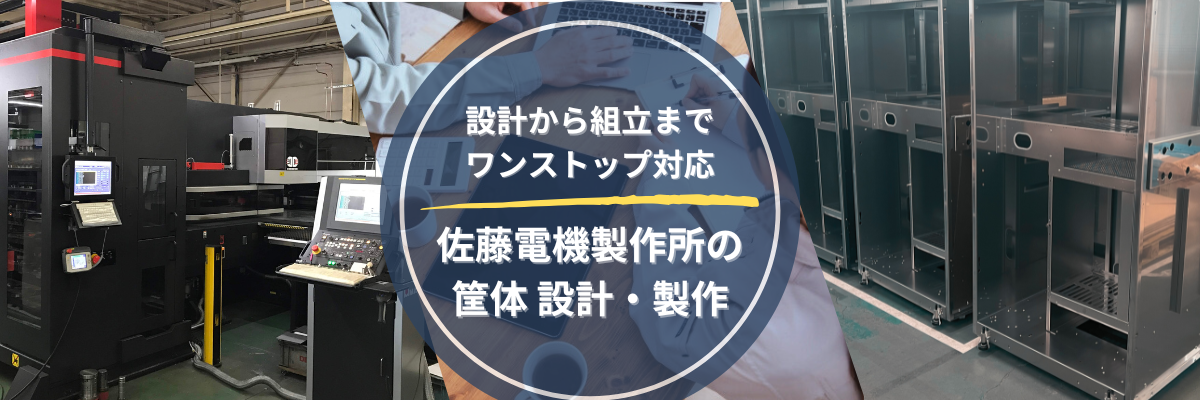
溶接不良の種類と原因
溶接不良には、様々な種類があります。主な種類と原因を以下に示します。
外観不良
スパッタ: 溶接時に発生する金属の飛散物。1
ビード形状不良: 溶接ビードの形状が不均一、凹凸、蛇行など。
アンダーカット: 溶接金属が母材に十分に溶け込まず、溝状に欠損した状態。
オーバーラップ: 溶接金属が母材の上に盛り上がりすぎた状態。
内部欠陥
ブローホール: 溶接金属内部に気泡が残った状態。
クラック: 溶接金属や熱影響部(HAZ)に亀裂が入った状態。
スラグ巻き込み: 溶接時に発生するスラグが溶接金属内部に巻き込まれた状態。
溶込み不足: 溶接金属が母材に十分に溶け込んでいない状態。
これらの溶接不良は、以下のような要因によって発生します。
溶接条件: 溶接電流、電圧、溶接速度などの溶接条件が不適切な場合。
母材: 母材の材質、表面状態、板厚などが溶接に適さない場合。
溶接材料: 溶接棒、溶接ワイヤなどの溶接材料が母材に適さない場合。
溶接姿勢: 溶接姿勢が悪いと、溶接金属が適切に流れず、溶接不良が発生しやすくなります。
作業環境: 温度、湿度、風などの作業環境が溶接に適さない場合。
作業者の技能: 溶接作業者の技能が未熟な場合。
溶接不良が引き起こす問題点
溶接不良は、筐体の品質や性能に様々な悪影響を及ぼします。主な問題点を以下に示します。
強度低下: 溶接不良があると、溶接部の強度が低下し、筐体全体の強度不足につながります。
耐久性低下: 溶接不良箇所は腐食が発生しやすく、筐体の耐久性を低下させます。
外観不良: スパッタやビード形状不良など、外観を損なう溶接不良が発生する可能性があります。
気密性・水密性不良: 溶接不良があると、筐体の気密性や水密性が損なわれ、内部に水分や異物が侵入する可能性があります。
安全性低下: 溶接不良によって筐体が破損した場合、重大な事故につながる可能性があります。
溶接不良を防ぐための対策
溶接不良を防ぎ、高品質な溶接を行うためには、以下の対策を総合的に実施することが重要です。
設計段階での対策
溶接しやすい形状を設計する。
溶接箇所を減らす。
適切な溶接方法を選択する。
溶接部の強度を十分に確保する。
材料選定
溶接に適した材質を選択する。
母材の表面状態を確認し、必要に応じて清浄化する。
溶接条件の設定
溶接電流、電圧、溶接速度などを適切に設定する。
溶接条件を記録し、品質管理に役立てる。
溶接材料の管理
適切な溶接材料を選択し、保管状態を適切に管理する。
使用期限内の溶接材料を使用する。
作業環境の整備
溶接作業を行う場所の温度、湿度、風などを適切に管理する。
溶接時に発生する煙やガスを適切に排気する。
作業者の教育
溶接作業者に対して、適切な溶接技術、安全教育を実施する。
資格取得を奨励し、技能向上を図る。
溶接後の検査
目視検査: 溶接部の外観を目視で検査し、スパッタ、ビード形状不良、アンダーカット、オーバーラップなどの有無を確認する。
非破壊検査: 溶接部の内部欠陥を検査する方法。放射線透過試験(RT)、超音波探傷試験(UT)、磁粉探傷試験(MT)など、様々な方法があります。
破壊検査: 溶接部の一部を切断し、その断面を検査する方法。溶接部の強度や溶け込み状態を確認することができます。
溶接不良に関する事例と対策
事例1: 薄板の溶接で溶け落ちが発生
原因: 溶接電流が大きすぎる、溶接速度が遅すぎるなどが考えられます。
対策: 溶接電流を下げる、溶接速度を上げる、裏当て材を使用するなどの対策が有効です。
事例2: 溶接部にクラックが発生
原因: 溶接時の入熱量が大きすぎる、溶接後の冷却速度が速すぎる、母材に水素が侵入しているなどが考えられます。
対策: 溶接入熱量を適切に制御する、予熱・後熱を行う、低水素系溶接材料を使用するなどの対策が有効です。
筐体製作における溶接不良対策のポイント
筐体製作では、特に以下の点に注意して溶接不良対策を行う必要があります。
外観品質: 筐体は見栄えが重要な要素となるため、外観を損なう溶接不良は避けなければなりません。スパッタ防止対策や適切な溶接条件の設定、溶接後の仕上げ処理など、外観品質向上のための対策を徹底する必要があります。
気密性・水密性: 筐体が内部に電子部品などを収納する場合は、気密性や水密性を確保する必要があります。溶接不良があると、そこから水分や異物が侵入し、故障の原因となる可能性があります。溶接部の気密性・水密性試験を行い、問題があれば修正する必要があります。
コスト: 溶接不良が発生すると、手直しや再加工が必要となり、コスト増加につながります。溶接不良を未然に防ぐための対策を講じることが、コスト削減につながります。
まとめ
溶接不良は、筐体の品質や性能に深刻な影響を及ぼす可能性があります。設計段階から溶接不良対策を考慮し、材料選定、溶接条件の設定、作業環境の整備、作業者の教育など、様々な対策を総合的に実施することが重要です。また、溶接後の検査を適切に行い、溶接不良を早期に発見し、修正することも重要です。