筐体設計でよくあるトラブルとその解決策
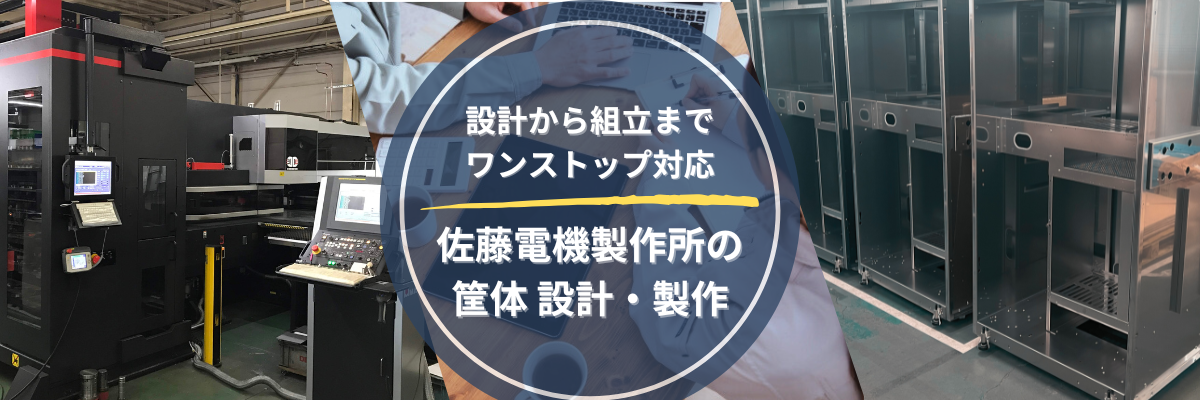
筐体とは
筐体とは、機器や装置を外部から保護するための外装部分を指します。
内部の電子部品や機械的な構造を、外部環境の影響から守る重要な役割を果たしており、防塵や防水、耐衝撃性、耐熱性、耐腐食性といった性能が求められます。
これらの特性は、製品が使用される環境に応じて異なるため、設計段階で慎重に考慮されるべき要素です。筐体は単なる保護機能に留まらず、製品の機能性や耐久性、美観にも大きく関わる重要な要素となっています。
筐体設計とは
筐体設計は機械設計の重要な一分野であり、製品の機能や性能要件を満たしながら、同時に製造コストや生産性も考慮しなければなりません。例えば、電子機器の筐体では防塵性や放熱性、耐震性などの必須項目のほか、外観品質も求められる場合があり、表面処理が必要になることが多々あります。
また、筐体設計では製作工程を最適化することも求められます。例えば部品点数の削減や工程の短縮によって、量産時のコスト削減や納期短縮につながる提案をすることが求められます。
筐体設計によくあるトラブルとその解決策とは
筐体設計を考える上で、よくあるトラブルとその解決策を、筐体設計を得意とする当社の視点からご紹介します。
⓵図面が平面図だとわかりにくい
筐体設計において、図面を一枚の平面でお客様に提案しますと、複雑な構造や細部の理解が困難になる場合があります。
これは特に量産を視野に入れた際に問題となり、製造効率や品質管理に影響を及ぼす可能性があります。当社では、この課題に対して3D設計技術を活用した提案を行っています。3Dモデルを用いることで、製品の全体像や各部品の関係性を視覚的に把握しやすくなり、設計の最適化が容易になります。
さらに、この手法を通じて、一見して一体型に見える筐体でも、実際には分割製造が有利な場合があることを明確に示すことができます。
例えば、ある案件では、当初一枚で設計されていた筐体を複数のパーツに分割することを提案しました。
これにより、製造工程の簡略化、材料コストの削減、そして納期の短縮を実現しました。3D設計を活用したこのアプローチは、クライアントの製品競争力向上に大きく貢献しています。
②一品生産と量産の製造方法の違い
筐体設計において、一品生産と量産では製造方法が大きく異なる場合があります。
一品生産では高度な加工技術や特殊な材料を使用できる一方、量産ではコスト面と生産性を重視する必要があります。当社では、この課題に柔軟に対応できる体制を整えています。一品生産と量産の両方に対応可能な設計ノウハウと製造設備を有しており、お客様のニーズに応じて最適な提案を行います。具体的な解決策として、材料の変更を提案することがあります。例えば、一品生産で使用していた高価な材料を、量産時には同等の性能を持つより安価な材料に置き換えることで、コストダウンを図ります。また、製造方法の変更も効果的です。溶接で接合していた部分をリベット接合に変更したり、一品生産時に使用していた特殊な加工を、量産時にはより簡易なカシメ加工に変更したりすることで、製造コストの削減と納期の短縮を同時に実現できます。
当社の板金筐体 設計・製作サービスの3つの特長
① 設計段階からのコストダウン提案で試作から量産まで対応
佐藤電機製作所の精密筐体フレーム・ファクトリーでは、図面作成時から材質や加工方法の見直しを提案し、コスト削減と品質向上に貢献しています。設計変更を通じて、製造コストの低減や納期短縮を実現し、年間100件以上の改善提案をもとに、試作から量産まで様々なニーズに柔軟に対応しています。
② 最先端設備を駆使した高品質な加工プロセス
佐藤電機製作所の精密筐体フレーム・ファクトリーでは、曲げ加工やレーザー加工、プレス加工、溶接に加え、メッキ、塗装、印刷、部品調達、組立、出荷まで一貫生産体制を整えています。各工程でデータを効率的に管理し、安定した品質とコストパフォーマンスの高い製品を提供しています。
③ 多品種少量生産を支える安定した生産体制
佐藤電機製作所では、西関東エリアにある最先端設備と生産管理システムを活用し、工程進捗を徹底管理しています。
また、図面の電子化とタブレットによるデータの可視化により、納期遵守率97%を達成しています。
多品種少量生産にもスピーディーかつ柔軟に対応し、10~100個規模の製品を短納期でコスト効率良く提供しています。
当社の業界ごとの筐体設計・製作事例をご紹介!
事例1 キャビネット(精算機)
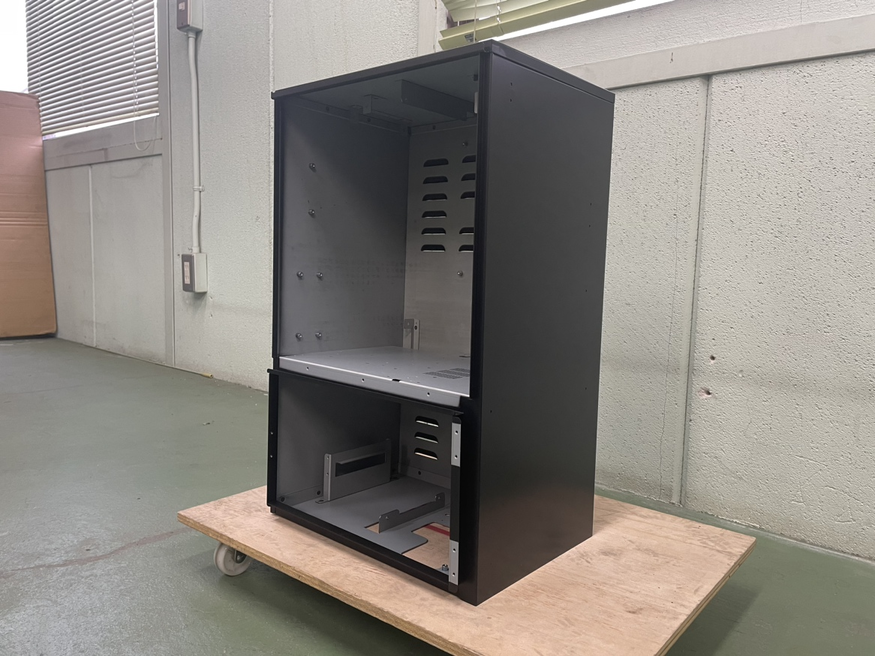
こちらは、精算機に用いられるキャビネットの製作事例です。この製品は、スポット溶接を行う箇所を事前にエンボスで位置決めを行っています。そのためズレのない精度の高い製品に仕上げています。
>>詳しくはこちら
事例2 半導体製造装置 筐体
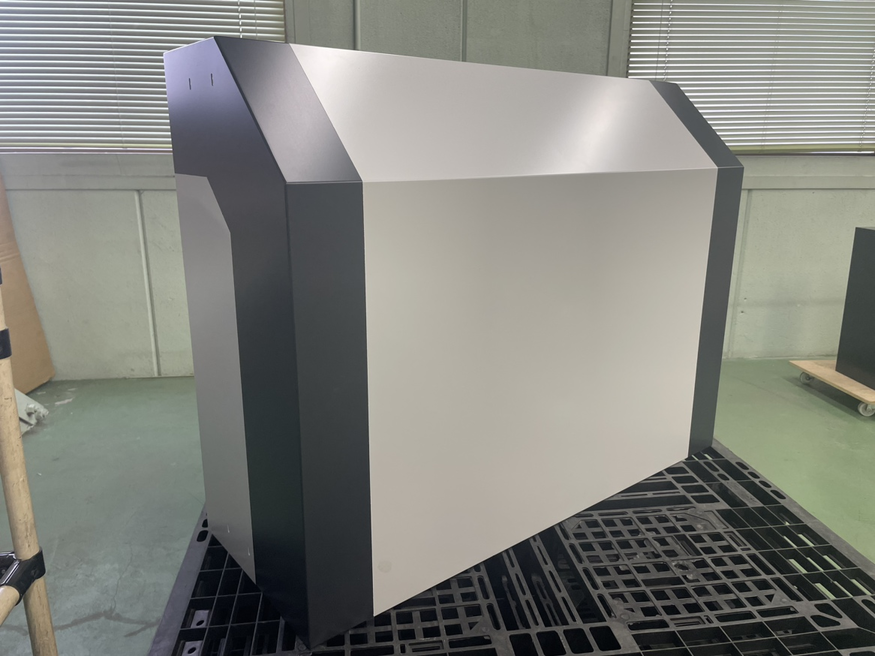
こちらは、半導体製造装置の外装部品の製作事例です。この製品の特長は材質がアルミという点です。アルミは熱伝導性が高く、溶接加工の難易度が非常に高い金属です。当社では、溶接速度が速く溶接個所以外に熱を伝えにくい加工ができる、ファイバーレーザー溶接機を保有しているためアルミの溶接加工も行うことが出来ます。加えて、ファイバーレーザー溶接はビードの幅に対して溶け込みが深いことから歪みを抑えた製品を製作可能です。
>>詳しくはこちら
事例3 OCR筐体
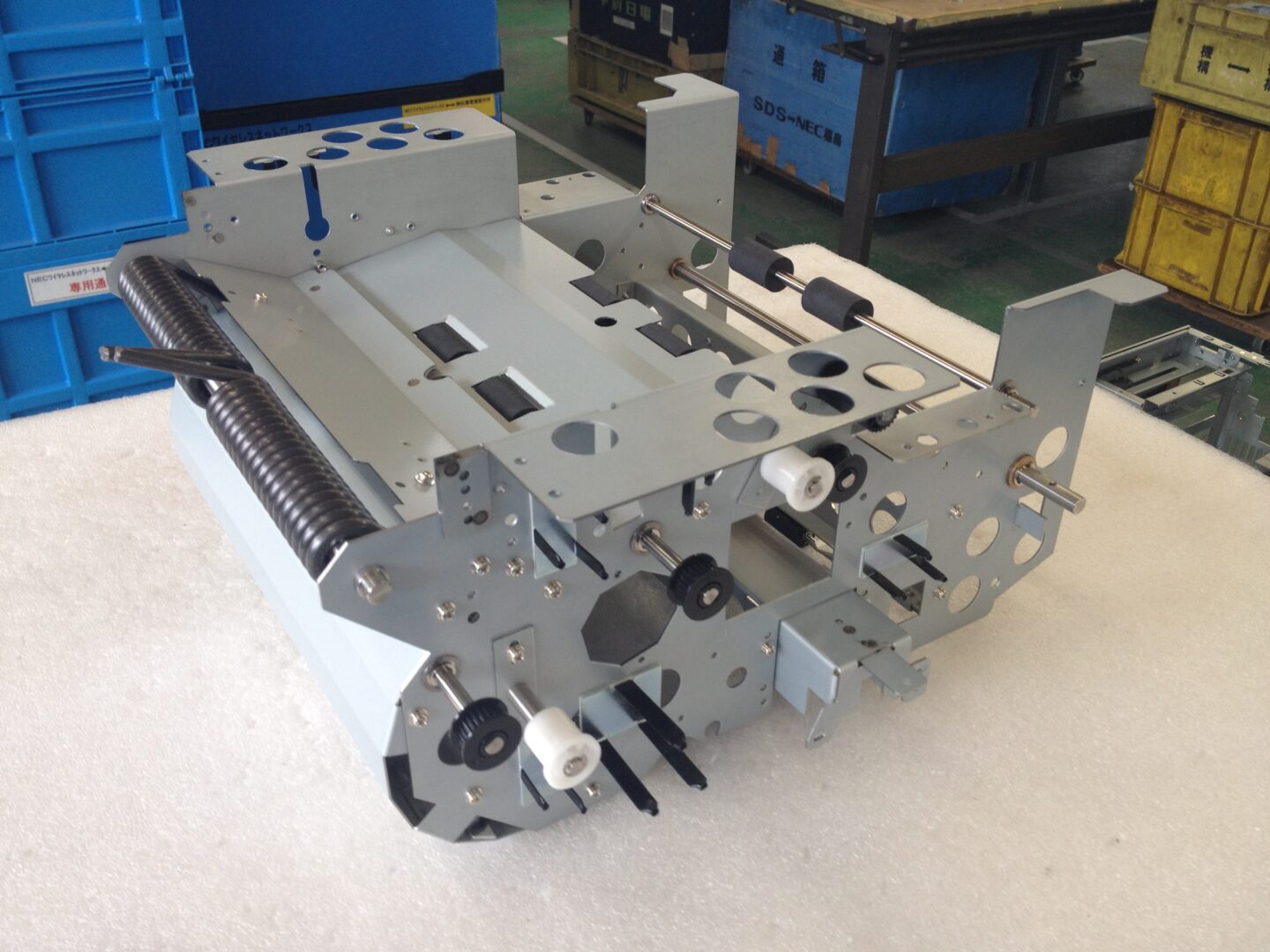
こちらは、OCR筐体の製作事例です。OCR筐体の製作は、紙にキズを付けず、文字を読み取るため、精密な加工が必要となっています。当社は、部品のバリ取りと細かい曲げ加工を行い、キズのないよう製作しております。
また、組立の段取りが多いため、細心の注意を払った組立てを行っています。
>>詳しくはこちら
最後に
精密筐体・フレームファクトリーを運営する佐藤電機製作所は、過去多くの精密板金筐体の設計・製作をしてきました。当社はそのノウハウから、通常だと時間のかかる溶接を行う箇所をリベット接合に変更するなど柔軟な納期に対応できるような体制を整えています。
他にも最小の歪みで製作したい、短納期で対応してほしいなど、些細なことでも是非一度当社にご相談ください。
>>お問い合わせはこちら