半導体検査装置用の筐体設計・製作のポイント
筐体とは
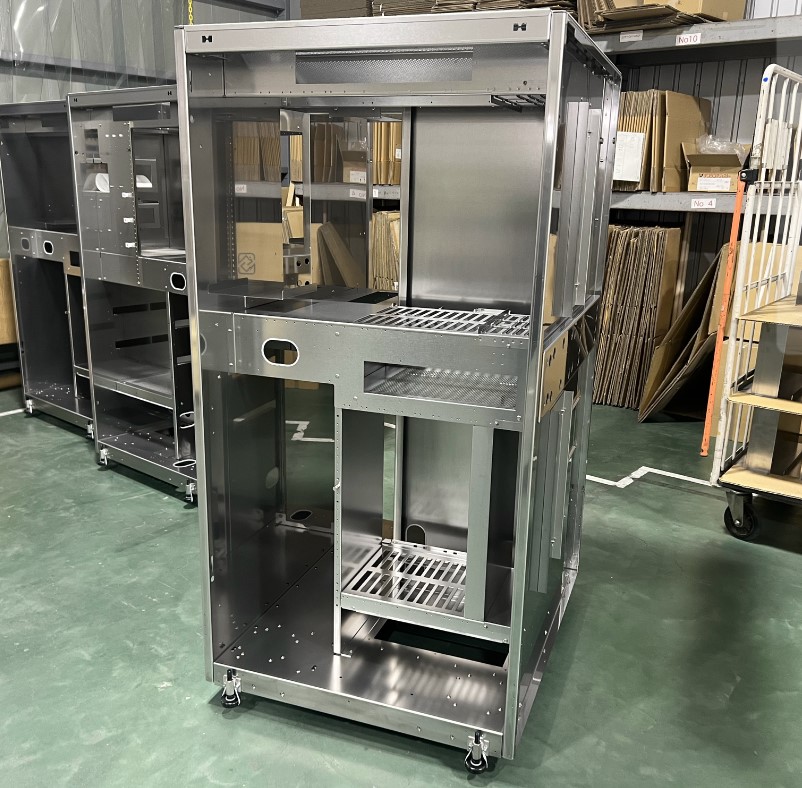
筐体とは、機器や装置を外部から保護する外装部分を指します。内部の電子部品や機械要素を外部の影響から守り、防塵、防水、耐衝撃、耐熱、耐腐食などの性能が求められます。これらの特性は、製品が使用される環境に応じて異なるため、設計段階での慎重な検討が不可欠です。筐体は、製品の外観だけでなく、機能性や耐久性にも大きな影響を及ぼす重要な部品です。筐体というくくりの中には、スマートフォンなどの小型のものから、半導体検査装置用の大型の筐体など、様々なサイズのものが該当します。
本記事では、半導体検査装置用の筐体についてご紹介します。
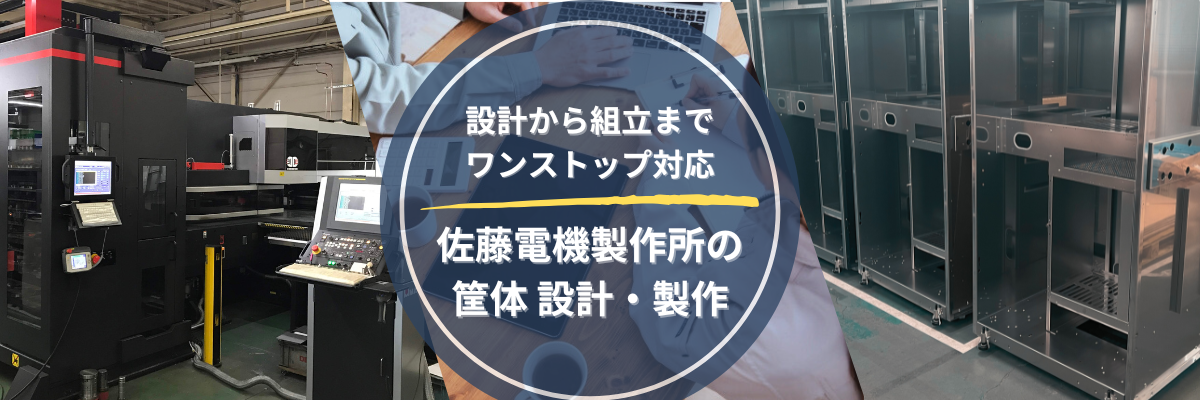
半導体検査装置の筐体設計・製作において特に求められること
私たちは、長年半導体検査装置の筐体を製作してきましたが、
⓵品質、②コスト、③納期の3つがお客様に特に求められています。
品質
半導体業界における品質基準は極めて高く、筐体の設計・製作においても最優先事項となっています当社では高品質の筐体を設計・製作するためには下記のことを徹底しています。
⓵高精度な温度管理
半導体デバイスは特定の温度範囲内で正確に動作するため、筐体内部の温度管理が極めて重要となります。当社では、放熱性の高いステンレス鋼(SUS430、SUS304)を使用し、細部には全て社内制作しているパンチングメタル加工やルーバー加工を用いて効率よく放熱が出来るように設計・製作しております。
②外観品質
人目につく製品が多いため、外観の品質に対する要求が非常に高いです。必要に応じてテープ付き材料の使用やレーザー・パンチ複合機でのブランク加工時の裏面キズ防止対策、加工時の取り回し方の徹底等、高い外観品質を維持しています。
コスト
半導体業界は競争の激しい業界であり、半導体検査装置用の筐体も例にもれず、コスト面というのは重要視されます。
当社では品質を保ちながらコストダウンを図るために、下記のことを徹底しています。
⓵効率的な製造プロセス
当社では、リベット接合で接合しても仕様上問題がない箇所はリベット接合にすることで、熟練技術者が必要な溶接加工に比べて作業時間を大幅に短縮しています。
溶接工程に比べて、スペースを取らず作業スピードも早いため、溶接コストの削減を実現しています。
②材料の最適化
放熱性と耐久性のバランスを考慮し、ステンレスを主に使用しています。ステンレスは耐久性も高く、長期間の使用ができるため、長い観点から見るとコストダウンにつながります。
また、材料の豊富な知識もございますので、SUS430、SUS340に縛られない使用用途にあった材料のご提案をしています。
③多品種生産への対応
図面や作業手順書の電子化により、多品種生産に伴う複雑な工程管理を効率化しています。弊社では全社員がiPadを所有しており、様々なデータやノウハウを電子で保存していることから、いつでもどこでも製造者が確認、検査作業をすることが可能となっています。そのため、多品種小ロットの生産にも対応しています。
納期
半導体業界はほかの業界と比べ、急速な技術進化をしています。その急速な技術進化に対応するために、迅速な製品開発と納品が求められます。当社では高い納期遵守率を保つために、下記のことを徹底しています。
⓵柔軟な生産体制
リベット接合の採用により一人一日5台以上組立が可能になるため、急な納期変更にも柔軟に対応できる体制を整えています。これにより、顧客の要求に迅速に対応することが可能となっています。
②効率的な情報管理
図面や作業手順書を電子化し、設備と生産管理システムがリンクしているため、一元管理システムが可能となっています。これにより、生産プロセスの効率化と納期短縮を実現しています。
このように当社では、設計から製造までの時間を短縮し、納期の遵守を確実にしています。当社の半導体検査装置用筐体は、お客様の厳しい要求に応える製品として高い評価を得ています。
当社の板金筐体 設計・製作サービスの3つの特長
① 設計段階からのコスト削減提案で試作・量産に対応
佐藤電機製作所の精密筐体フレーム・ファクトリーでは、図面の作成時点から材質や加工方法の最適化を提案し、コストダウンや品質の向上を実現しています。これにより、製造コストの削減や納期の短縮を目的とした設計変更が可能で、年間100件以上の改善提案を通じて試作から量産まで幅広いニーズに対応しています。
② 最新設備を活用した高品質な加工
佐藤電機製作所の精密筐体フレーム・ファクトリーでは、ブランク加工、曲げ加工、溶接加工、組立から、メッキ、塗装、印刷、部材調達、出荷まで一貫して行う体制を整えています。各工程のデータを効率的に管理・活用することで、安定した加工品質と高いコストパフォーマンスを実現し、お客様の要望に応える製品を提供しています。
③ 安定した生産体制で多品種少量生産を実現
西関東エリアにおける最先端設備を有する佐藤電機製作所は、生産管理システムにより工程進捗を管理し、図面の電子化とタブレットを活用したデータ可視化を通じて納期遵守率97%を達成しています。このような安定した生産体制により、多品種少量生産に柔軟に対応し、10~100個規模の製品を最適なコストと短納期で提供しています。
当社の業界ごとの筐体設計・製作事例をご紹介!
事例1 半導体検査装置用 ステンレス筐体
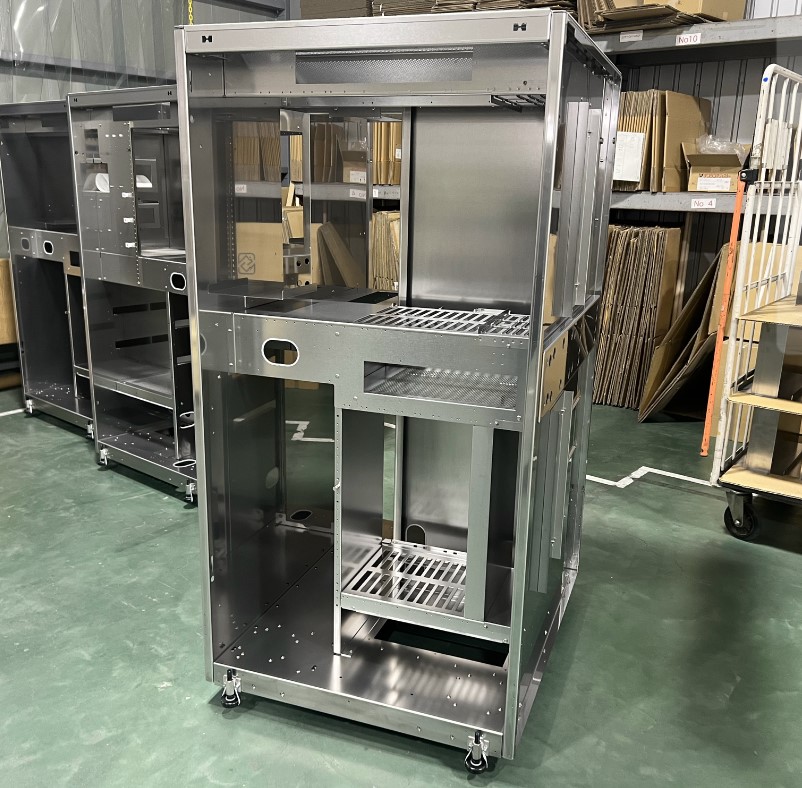
こちらは、半導体検査装置 筐体の製作事例です。本来は、溶接で接合を行うような筐体でしたが、月産100個を超える生産が必要だったため、溶接からリベット接合に変更いたしました。また、お客様から依頼いただいた段階では、SUS430 2B材を使用予定でしたが、製品の仕様をヒアリングし、SUS430KDに変更提案をし、コスト削減を実現しています。
>>詳しくはこちら
事例2 半導体検査装置 ステンレス筐体
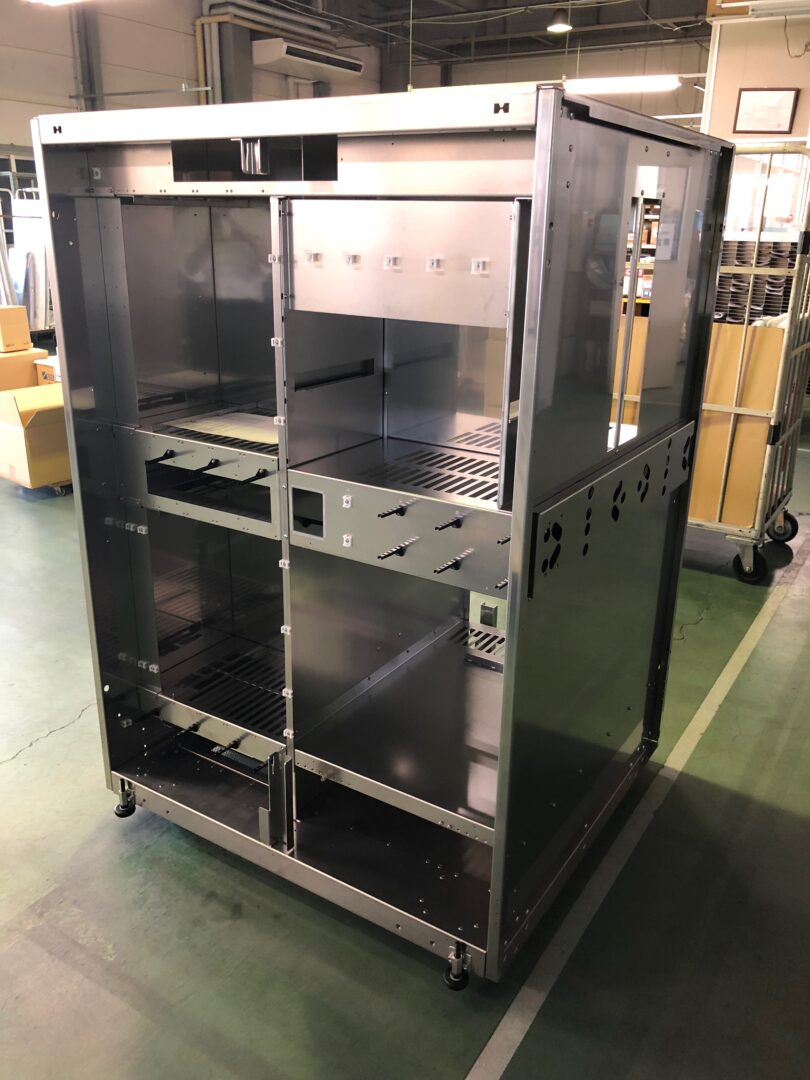
こちらは、半導体製造検査装置の筐体です。バリなしのレーザー加工によりバリ取り作業の削減、バーリング、タッピング、成形加工などの自動化により、作業時間が短縮され、品質が向上しました。
更に、溶接を使わないリベット式構造の採用により、製品の歪みを最小限に抑えています。リベット式構造は溶接に比べ、場所を取らず、修正も容易であるため、大きな製品でも必要な時に必要な分だけ生産することが可能です。
また、当社ではワンストップ生産に対応しているため、ブランクから組み立て、梱包、発送まで一貫して行われ、高品質で低価格な製品が提供されています。
>>詳しくはこちら
事例3 半導体製造装置 外装
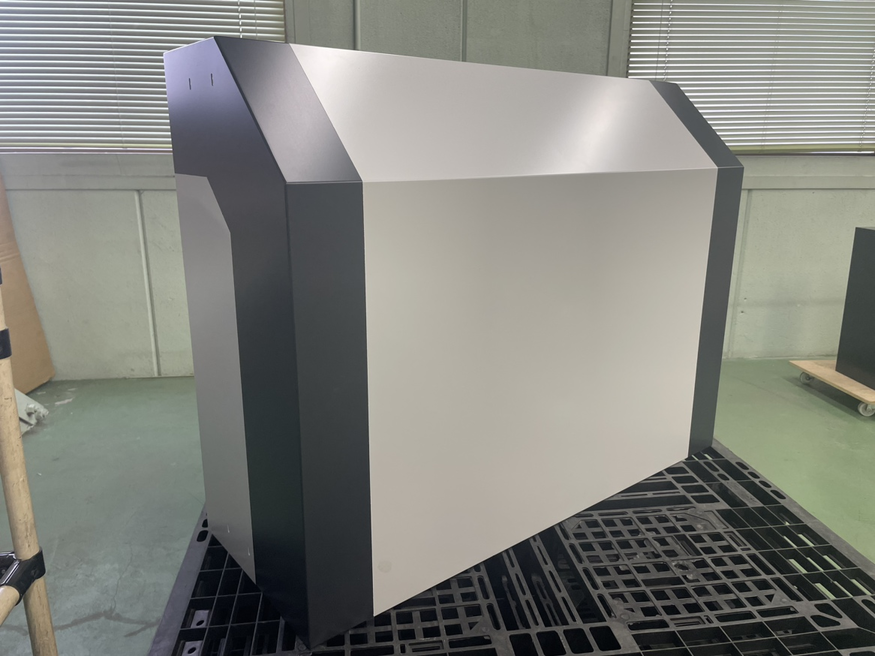
こちらは、半導体製造装置の外装部品の製作事例です。この製品の特長は材質がアルミという点です。アルミは熱伝導性が高く、溶接加工の難易度が非常に高い金属です。当社では、溶接速度が速く溶接個所以外に熱を伝えにくい加工ができる、ファイバーレーザーロボット溶接機を1台、ハンディタイプを2台保有しているため、薄板のアルミの溶接加工も難なく行うことが出来ます。加えて、ファイバーレーザー溶接はビードの幅に対して溶け込みが深いことから歪みを抑えた製品を製作可能です。
>>詳しくはこちら
事例4 半導体製造装置 外装
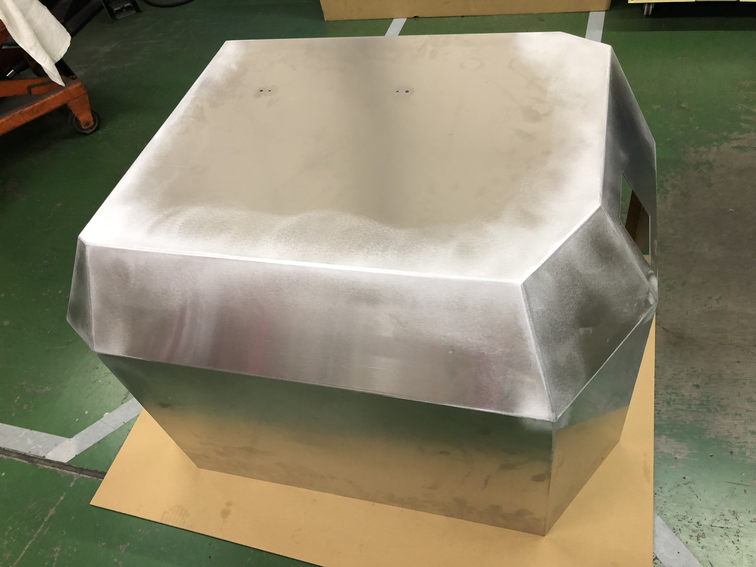
こちらも、別の半導体製造装置の外装部品製作事例です。こちらの製品は材質はアルミであり、複雑な多面体となっています。上部に見えている部分は面を組み合わせて溶接するため、歪みの少ない加工が求められます。従来のTig溶接ですと、形作ることさえ難しい製品でしたが、ファイバーレーザー溶接を使うことで、綺麗に素早く加工することが可能となっています。
>>詳しくはこちら
筐体の設計・製作なら当社にお任せください
精密筐体・フレームファクトリーを運営する佐藤電機製作所は、過去多くの精密板金筐体の設計・製作をしてきました。当社はそのノウハウから、通常だと時間のかかる溶接を行う箇所をリベット接合に変更するなど柔軟な納期に対応できるような体制を整えています。他にも最小の歪みで製作したい、短納期で対応してほしいなど、些細なことでも是非一度当社にご相談ください。
>>お問い合わせはこちら